Solucionamos los problemas de fugas en los ensamblajes de puertas de automóvil
Scanning and Inspection Pty recurre a PolyWorks® y analiza la relación entre el marco de la puerta y la carrocería del automóvil en menos de 1 hora.
Los fabricantes saben cuándo algo sale mal y averiguar por qué suele ser un proceso mucho más complicado. El proceso de investigación consiguiente consume tiempo, dinero y recursos. Incluso una vez que el problema se ha identificado finalmente, hacer ajustes cuantificados es otra etapa en el camino hacia la rectificación. A veces la pieza fabricada es diferente de la pieza diseñada, o diferente de cómo debería ser o ha sido anteriormente, pero ¿en qué medida, dónde y en qué dirección? Para un importante fabricante de automóviles australiano, identificar la causa de las fugas en los ensamblajes de las puertas era una prioridad.
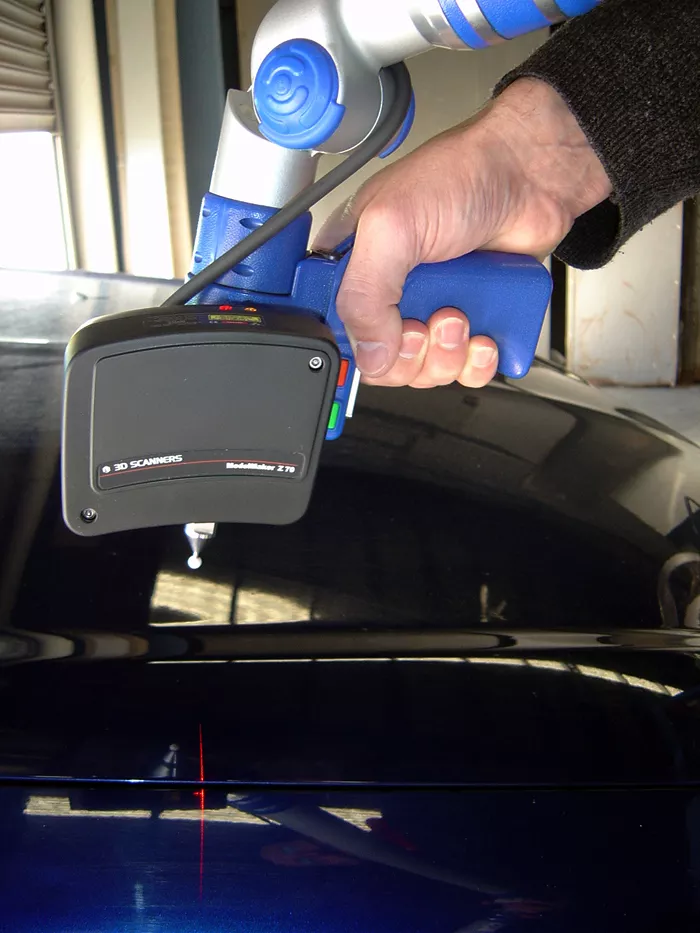
ModelMaker Z70 montado en un FaroArm
El desafío
Un fabricante de automóviles experimentó recientemente una de esos situaciones inevitables de fabricación. Encontraron variaciones en la alineación de ciertos sellos de las puertas de la cabina de pasajeros que produjeron y ensamblaron. Era evidente que ciertos automóviles que se habían fabricado durante una etapa específica de la producción del automóvil quedaron como se esperaba, las puertas y los sellos estaban alineados con el resto de la carrocería del automóvil a la perfección. Sin embargo, aquellos que salieron de la línea de producción en una etapa posterior tenían fugas de agua durante la etapa de prueba. La primera tarea consistió en localizar por dónde pasaba el agua, pero lo más complicado de analizar era la relación entre el marco de la puerta y la carrocería del automóvil. Sin embargo, descubrir qué era diferente a los vehículos que no tenían fugas y determinar en qué medida, dónde y en qué dirección planteaba una serie de desafíos.
Si un lote de ensamblajes automotrices salió de producción y no experimentó problemas de fugas y otros producidos en una etapa posterior tenían fugas, entonces de alguna manera deben diferir en su estructura. ¿En qué se diferencia el ensamblaje del marco de la puerta que presenta problemas del que no los presenta? Para saber qué cambios deben realizarse durante la producción, el cliente debe poder cuantificar la discrepancia. Es necesario evaluar la relación y las variaciones entre los ensamblajes de marco de puerta ‘buenos’ y ‘malos’. Se adquirió un análisis comparativo detallado y, gracias a la última tecnología de escaneo láser y a la suite de PolyWorks®, se logró en cuestión de horas.
La solución
Adquisición de datos
Para capturar de manera rápida y eficiente la información de la superficie, los especialistas de Scanning and Inspection utilizaron un escáner láser montado en un brazo articulado. El tipo de escáner láser utilizado para esta aplicación fue el ModelMaker Z70, un escáner de alta calidad capaz de digitalizar una superficie con una densidad notable de 0.05 mm x 0.05 mm, que es alrededor de 400 puntos por milímetro cuadrado. Esto da como resultado una representación digital 3D realista y completa de la pieza, una enorme cantidad de datos que se pueden transformar en información útil. El escáner obtiene su referencia 3D de una CMM portátil, en este caso un Platinum FaroArm, que mide con una repetibilidad de ± 0,0051 mm dependiendo de su tamaño. El FaroArm y el escáner láser MMZ70 se colocaron en su lugar en el lugar gracias a un trípode de alta resistencia, por lo que el hardware se pudo instalar convenientemente junto a las puertas del automóvil en cuestión. La captura de los datos de la superficie que se requerían tomó solo unos minutos por automóvil.
El proceso de PolyWorks
Una vez que se recopilaron los datos de escaneo, comenzó la etapa de posprocesamiento del análisis. Con PolyWorks, los especialistas de Scanning and Inspection Pty Ltd. alinearon virtualmente los datos escaneados con láser del automóvil con fugas con el del automóvil sin fugas, y realizaron análisis avanzados de medición y comparación. Sin embargo, antes de realizar los análisis comparativos, se tuvo que realizar una serie de manipulaciones de nubes de puntos en PolyWorks.
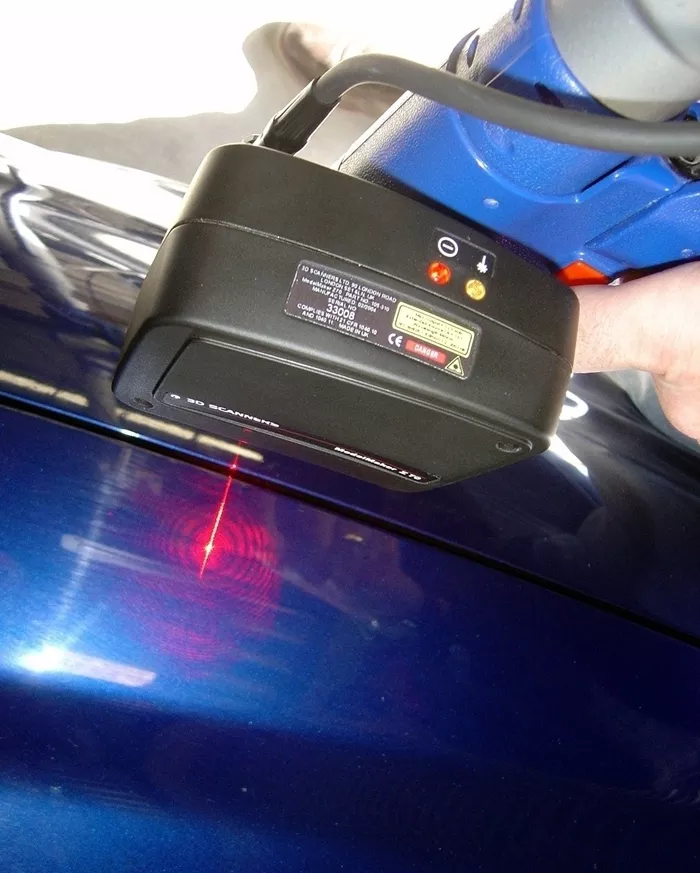
Adquisición de datos
Refinar la alineación del escaneo
Durante la etapa de adquisición de datos del trabajo, se obtuvieron varias pasadas de escaneo. Cada parche de escaneo se alinea automáticamente utilizando la tecnología de alineación nativa del brazo articulado que proporciona la referencia espacial para la ubicación cambiante del escáner láser. La mayoría de las nubes de puntos adquiridas por el escáner láser se colocan “encima” de las otras que ya se han tenido en cuenta en otras pasadas del escáner. Por tanto, determinadas partes de la pieza se miden más de una vez. Estas áreas de datos de varios niveles se denominan áreas de superposición.
Para refinar la nube de puntos alineados obtenida de la CMM portátil, el módulo PolyWorks IMAlign utiliza estas áreas de superposición para realinear todos los escaneos. Primero, se realizó un análisis de desviación en la nube de puntos alineada. PolyWorks calcula automáticamente las distancias promedio entre cada escaneo superpuesto y muestra un color que representa un valor de desviación. Con un vistazo, los usuarios pueden identificar los escaneos que están fuera de tolerancia y que pueden mejorarse con la realineación.
Luego, se realizó una realineación con la tecnología de alineación de “mejor ajuste” de PolyWorks. Para evitar el “deslizamiento” entre parches en el mismo entorno, automáticamente se establecen ocho puntos de control para cada escaneo, lo que restringe los grados de libertad. Esta función diferencia a PolyWorks de otras soluciones de alineación de escaneo, que a menudo encuentran problemas de deslizamiento durante la alineación de escaneo. Una vez realizada la alineación de mejor ajuste restringida, se calcula un nuevo análisis de desviación y se muestra un mapa de color.
El último paso consiste en crear un modelo de nube de puntos de una sola capa promediando de manera inteligente todos los escaneos superpuestos utilizando la tecnología de “reducción de superposición” de PolyWorks. La nube de puntos resultante ahora se puede transformar en una superficie que se utilizará para análisis posteriores, como comparaciones entre puertas. La metodología de escaneo fue la misma tanto para los autos con fugas como para los que nos las presentaban. Se quitaron todos los recortes periféricos de los marcos de las ventanas y de las puertas para exponer solo los componentes de acero estructural de posproducción. Las puertas se cerraron durante todo el proceso de captura de datos y las áreas relevantes asociadas con los sellos con fugas se escanearon con el láser MMZ70.
Cuando la franja del láser se movió por la superficie, recolectando decenas de miles de puntos 3D por segundo, la superficie subsiguiente apareció inmediatamente en la pantalla de la computadora. Las capacidades de esta visualización de la superficie de la nube de puntos en tiempo real significaron que las áreas que se pasaron por alto, o que aún no se escaneaban, podían identificarse al momento de realizar la medición y, en consecuencia, tomarse en cuenta.
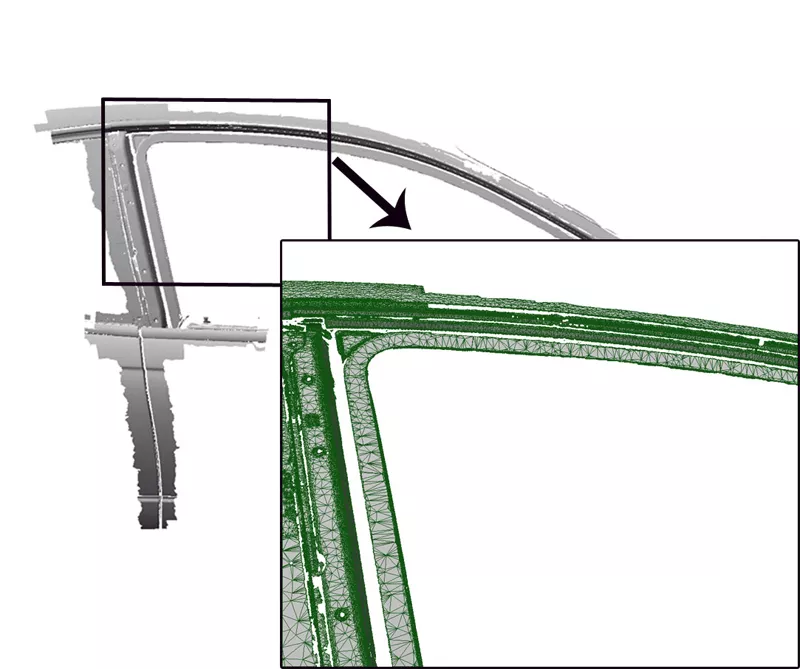
Creación de un modelo poligonal
Crear un modelo poligonal
Con el fin de comparar las superficies de los ensamblajes de marco de puerta “buenos” y “malos”, el escaneo y la inspección necesitaban convertir las nubes de puntos en algo que se pudiera usar como una superficie. PolyWorks convirtió las decenas de millones de puntos de la nube de puntos en una malla triangulada en un abrir y cerrar de ojos. El software utilizó cada uno de los puntos como nodos para los millones de triángulos diminutos que construyó.
Para describir con precisión las diversas formas del objeto escaneado, PolyWorks usa menos triángulos para las secciones más consistentes de la superficie del automóvil y más triángulos cuando el contorno se vuelve complejo, todo en función de los valores de tolerancia que especificó el usuario. Los parámetros de distancia de búsqueda y del vecino más cercano también se estipulan antes de la conversión y para crear la superficie triangulada y reducir el ruido inherente del digitalizador al máximo.
Comparaciones entre las puertas
Usando una serie compleja de análisis de superficie y matemáticas de “número mínimo de cuadrados”, los dos conjuntos de datos de escaneo láser recientemente optimizados y triangulados se colocaron uno encima del otro y se alinearon utilizando la tecnología de alineación de mejor ajuste de PolyWorks. Luego, PolyWorks desarrolló un patrón de distribución codificado por colores que destacaba la comparación de los dos ensamblajes. El mapa de color de errores resultante permite distinguir fácilmente los patrones que identifican cómo la puerta del automóvil que tiene las fugas se relaciona con la puerta del automóvil que no las presenta.
El pilar B y las secciones inferiores de las puertas muestran un color verde claro (casi aguamarina) que indica una desviación por debajo de ±0.5 mm entre los dos juegos de puertas. Otras regiones, como el marco de acero de la ventana que está soldado a la propia puerta, se ilustran en verde, lo que equivale a una desviación de ±1-2 mm. Finalmente, la sección naranja, ubicada en el chasis del automóvil, también indica una desviación de ±1-2 mm.
En otras palabras, cuando los pilares B de los dos automóviles se alinearon a una distancia de 0.5 mm, los marcos de las ventanas del automóvil con fugas en realidad se colocaron entre 0.5 mm y 2 mm por debajo del vehículo que no era susceptible a fugas, un espacio, sin duda, suficientemente grande para que pase el agua.
Los beneficios
Los ingenieros de Scanning and Inspection realmente consideraron que sería mucho más fácil cambiar las soldaduras responsables de la posición del marco de la puerta que ajustar el chasis de alguna manera. La soldadura con la que el marco de la ventana se une con la puerta se ajustó para que el marco no quedara tan bajo (en comparación con la puerta que no presentaba filtraciones).
Todo el proceso de inspección de PolyWorks se realizó en menos de 1 hora.
Las conclusiones extraídas de la investigación concentraron principalmente las preocupaciones del cliente en el marco de la ventana del vehículo, o más específicamente en la forma en que se soldaba al ensamblaje de la puerta principal. Se realizaron los ajustes adecuados en relación con los tratamientos de soldadura para garantizar que el marco de la ventana ya no estuviera situado demasiado dentro de su posición ideal, como se describe en el diseño CAD inicial.
La precisión y flexibilidad del FaroArm y el escáner láser MMZ70, utilizados en combinación con el software PolyWorks de clase mundial, permitieron a este fabricante de automóviles:
- Identificar rápidamente la fuente del problema de filtraciones
- Medir con precisión la desviación física de los ensamblajes de puertas de automóviles “malos” en comparación con los “buenos” (en qué medida, dónde y en qué dirección)
- Modificar el proceso de ensamblaje ajustando la soldadura donde el marco de la ventana se une con la puerta
- Realizar todo el proceso de inspección en menos de 1 hora